1 可靠性仿真技术背景介绍
当前全球科技水平的不断提升使得航空航天、军事装备等行业得到空前发展。高科技产品功能结构复杂、系统组成庞大、研发周期长费用高、可靠性问题突出。传统的基于统计的可靠性设计分析方法,与性能设计专业技术体系不一致,在设计过程中难以相互融合,造成可靠性设计分析工作往往滞后于性能设计分析工作,可靠性设计分析难以对产品的设计状态产生真正影响。同时,传统的可靠性试验与评估方法需要大量新研产品进行试验,往往在研制后期才能开展。通过可靠性试验发现产品薄弱环节再进行设计更改,时间周期长并且代价较大。工程实践表明,传统的可靠性设计分析与试验评估方法,越来越难满足高科技产品高可靠长寿命的需求。
近年来,数字样机与虚拟仿真等相关技术发展迅速,国内外大部分科研机构都采用虚拟仿真技术进行产品三维建模装配与功能/性能分析,从而在设计阶段早期获得产品性能参数并改进设计。目前,将可靠性工作融入到产品设计和分析仿真过程,在工程上有着强烈的需求。可靠性仿真技术充分利用产品现有的功能/性能模型及相关CAD工具,以系统功能/性能模型为内核,以可靠性模型为外壳,联合各专业CAD工具建立综合集成环境,实现可靠性与性能一体化建模仿真,支持在设计阶段开展基于仿真的可靠性设计、分析与评价。可靠性仿真结果可以为可靠性与性能的协同设计与分析提供模型与数据支持。综上可知,可靠性仿真技术对于解决工程中可靠性设计与性能设计“两张皮”问题具有极高的实用价值。
1.1 设备可靠性仿真分析
对于设备来说,当前的发展趋势是利用可靠性仿真技术,建立产品可靠性仿真模型,支持在设计阶段开展基于仿真的可靠性设计分析与虚拟试验评估。可靠性仿真技术以各性能专业的仿真模型为基础,进一步考虑产品的寿命周期载荷、故障行为与故障机理以及工艺参数的散布特性,建立可靠性仿真模型,即基于可靠性的产品数字样机。在基于可靠性的数字建模、数据传递、拓延和试验仿真过程中,提升和验证产品的可靠性。
以液压伺服产品为例,其总体设计流程如图 1所示。图中展示了控制系统设计、液压系统设计与执行机构设计之间的耦合关系。其中,控制系统需要利用控制系统仿真(Matlab/Simulink)来辅助设计;液压系统需要利用液压系统仿真(AMESim)来辅助设计;执行机构需要利用多体动力学仿真(ADAMS)来辅助设计。
图1 液压伺服系统总体设计流程图及其可靠性仿真考虑的不确定性因素
液压伺服产品等机电产品,其生产制造与使用环境中存在着各种不确定性因素,例如加工制造误差、材料属性的分散性、元器件参数漂移以及随机环境载荷(温度、湿度与振动)等。这些不确定性因素会对机电产品的实际性能产生深刻影响。例如电子控制系统参数的累积误差,可能导致其控制输出响应超出规定值而发生故障;执行机构的制造安装误差与外界环境载荷作用,可能导致运动卡滞等严重故障。
机电产品传统设计分析方法,一般只关注标称状态下的性能响应,难以考虑内外不确定性因素影响下的性能散布特性,导致设计出来的产品可能面临较高的故障风险,无法保证其可靠性满足要求。可靠性仿真技术能够将各种不确定性因素引入到仿真模型中来,利用多种不确定性量化手段,实现对产品性能响应不确定性的度量,并且找出关键不确定性因素,通过控制这些不确定性因素达到提高产品可靠性水平的目的。
1.2 飞行器可靠性仿真分析
对于飞行器来说,其设计研制已经涉及到数十门学科,这些学科之间相互耦合,参数传递关系复杂。虽然各学科领域大都形成了各自的研究方法与仿真分析工具,但各学科之间缺乏沟通与联系,往往导致学科接口之间产生耦合问题,严重影响系统可靠性水平。因此,在设备可靠性仿真的基础上,还需要引入基于多学科的仿真分析手段,在系统级层面上进行性能与可靠性的仿真分析计算,确定各学科接口的薄弱环节,为提高系统可靠性打下基础。
飞行器总体设计流程如图 2所示。图中给出了气动专业、动力专业、结构专业与航迹规划专业的耦合关系,其中涉及的仿真模型包括气动专业的计算流体力学分析(CFD)、动力专业的数值推进系统仿真(NPSS)、结构专业的有限元分析(FEM)以及航迹规划专业的航迹仿真。
图2 飞行器总体设计流程图及其可靠性仿真考虑的不确定性因素
在飞行器的生产制造与使用环境中存在着各种不确定性因素,例如加工制造误差、材料属性的分散性以及随机载荷等。这些不确定性因素会对飞行器性能指标产生深刻影响,需要在研制过程中予以充分考虑。传统设计分析方法只进行有限飞行工况下的仿真分析,获得的仿真结果往往不能包络最恶劣的情况。可靠性仿真不仅考虑了飞行工况,还考虑了不确定性因素,因此可以在飞行器系统存在诸多不确定性因素时,向决策者提供高置信度的系统行为预测。例如,对于几何外形设计来讲,不确定性因素主要包括飞行器前部形状尺寸、主升力面形状尺寸以及舵面位置及形状尺寸等;而针对空气动力学分析,不确定性因素主要包括飞行马赫数与迎角等。这些不确定性因素将在各阶段仿真过程中沿着仿真模型的逻辑结构不断传播,导致后续仿真输出响应的不确定性。
可靠性仿真能够对各学科性能响应的不确定性进行量化。例如,通过灵敏度分析,判断其中对飞行器整体性能波动影响最大的不确定性因素;通过可靠性分析,对飞行器性能响应的散布特性进行预测。最后给出飞行器系统的薄弱环节,计算飞行器系统可靠性,为飞行器性能预测提供支撑,为设计改进提供建议。
因此,可靠性仿真技术以建模仿真手段为突破口,将可靠性设计融入到性能专业的设计流程中,从而将可靠性设计与性能设计真正关联起来,实现性能与可靠性一体化设计分析。
2 国内外最新进展和发展趋势
2.1 国外可靠性仿真技术的进展与趋势
a) 设备可靠性仿真技术
美国NASA的AMES研究中心通过C-MAPSS(商用航空推进系统仿真模块)建立飞机发动机系统模型,通过单元退化机理模型和响应面技术构建了发动机性能参数的退化模型。该方法可以应用单元退化机理来预测系统退化过程和寿命。
美国Sandia国家实验室开发了基于CAD/CAE的可靠性仿真分析工具,通过虚拟仿真和物理加速试验相结合,对微型机械等设备的关键薄弱环节进行定位和评价。美国马里兰大学CALCE研究中心针对电子产品(主要为印制电路板),提出了一种基于故障物理的可靠性建模仿真方法。该方法利用热仿真、振动仿真等虚拟仿真技术为故障物理模型提供输入参数,并基于最弱环理论预测电子产品的寿命。CALCE还根据该可靠性建模仿真方法开发了一种用于电子产品可靠性预计的软件工具——CalcePWATM,已经在NASA的航天飞船逃逸系统、HONEYWELL公司的AS900航空引擎电子控制系统等产品的可靠性评估中成功应用,并发挥重要的作用。
法国国家太空研究中心针对微机电系统(MEMS),结合环境试验获得的数据与建模仿真工具,提出了基于故障物理的一阶行为模型建模与仿真方法,目的是提升MEMS的可靠性水平。爱尔兰国家微电子研究中心提出应用仿真工具对微电子产品进行可靠性建模与仿真,在建模过程中考虑了电迁移与应力迁移等退化机理,并且给出了该项技术的具体应用案例。以色列飞机工业公司研制了一种可靠性、维修性分析工具——综合可靠性分析工具IRAT(IntegratedReliability Analysis Tool)。该工具能够充分利用各专业CAE/CAD工具,采用功能分析技术实现专业设计工作与可靠性设计工作的良好结合。
b) 系统级可靠性仿真平台
在可靠性建模仿真、不确定性量化及优化技术的平台化研究方面,国外已经形成了一些通用软件平台。这些平台一般是将CAE仿真工具(例如多体动力学软件ADAMS、有限元分析软件ANSYS、ABAQUS、电路仿真软件PSPICE、液压仿真软件AMESim等)有效集成起来,解决可靠性建模仿真与优化问题。美国Sandia国家实验室开发的通用优化算法平台DAKOTA,提供包含基于梯度计算的非线性规划、无需梯度计算的模式搜索法和遗传算法等的优化算法库,以及蒙特卡洛与代理模型等不确定性量化方法。NASA利用DAKOTA对航空飞行器进行了不确定性量化分析与可靠性优化设计。美国Engineous公司开发的综合性CAE平台Isight/Fiber能够快速联合各种仿真软件,将设计框架、优化算法、代理模型组织起来,有助于实施产品的多学科优化设计与分析。
总体来说,国外特别是美国的科研机构对于可靠性仿真技术的理论研究日趋完备,并且已经将该项技术推广到工程领域中,在航天飞船、飞机引擎与某些军用装备的研制中发挥了重要作用。未来以美国为首的西方国家将进一步研究基于故障物理的可靠性仿真方法,实现更加精确逼真的可靠性建模与仿真分析。
2.2 我国可靠性仿真技术的进展与趋势
我国对可靠性仿真技术的研究开展时间较晚,技术发展相对滞后,目前正处于蓬勃发展阶段,并且形成了一些创新成果,例如可靠性与性能一体化建模仿真方法等。国内越来越多的企业与科研院所在产品研制工作中开始发现可靠性仿真技术的工程实用价值,并对部分设备开展了可靠性仿真分析工作。针对系统级产品来说,国内对于考虑可靠性的多学科设计优化技术,目前大多停留在研究探索阶段,北航针对机电产品的机械、电子、液压学科之间的耦合特性,初步建立了可靠性与性能一体化仿真设计分析平台,但尚未开展大规模应用。未来我国可靠性仿真的技术发展及工程化应用前景十分广阔。
北京航空航天大学可靠性与系统工程学院提出了可靠性与性能一体化建模方法,考虑了产品内外因素对性能参数的影响,综合利用各种CAD工具构造联合仿真环境。在此基础上,将随机故障、环境扰动与参数偏差注入到性能模型中,构造系统性能可靠度与设计参数之间的仿真模型。针对天线收放机构、电液伺服阀等机电产品,将磨损、疲劳等退化机理注入到产品仿真模型中,实现了对其关键参数的退化过程仿真。
西北工业大学针对航空领域大型复杂运动机构,建立了可靠性协同仿真试验系统,联合三维辅助建模软件CATIA、有限元分析软件Nastran、多体动力学分析软件LMS Virtual.Lab等软件工具,实现运动机构典型失效模式的可靠性仿真分析和评估。
航天一院在可靠性仿真技术领域开展了深入研究,筹建了可靠性仿真与评价实验室,并且搭建了机械产品、电子产品与机电产品可靠性仿真平台,为各类型产品可靠性与性能一体化设计分析、可靠性试验与评价提供有效支撑。
3 总结与展望
工程实践表明,可靠性仿真技术能够在研制阶段发现产品薄弱环节,为设计改进提供有效支撑。与此同时,可靠性仿真技术还能为可靠性预计、可靠性虚拟试验与评价等提供模型支持。特别是对性能设计与可靠性设计“两张皮”问题,可靠性仿真也提供了一条很好解决途径。未来,该项技术必将随着虚拟仿真技术的不断发展而得到更加广泛的研究与应用。
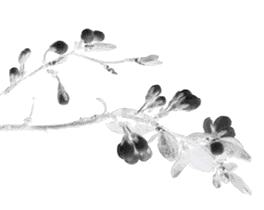
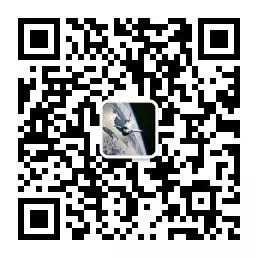
长按二维码识别关注我们