在我们日常的失效分析或者材料验证过程中,几乎都会有从单体电芯上拆解出极片,然后组装成扣电就行测试的经历,但是对于老化之后的电芯内部存在电极材料老化,电解液消耗,产气甚至料层剥离的现象,那么随后制作出来的扣电波动性就有可能会特别大,影响我们的测试分析过程。
对于拆解电芯及扣电制作过程我们需要注意些什么呢?
对于电芯拆解过程,我们会遇到形形色色种类电芯,容量也不尽相同,有时候会默认手套箱环境比较好,就保留了很多未使用的极片以待之后使用,但是这种做法是有问题,即使在含水氧含量很低的手套箱中,电极片也会与微量的水或氧发生反应,甚至与电解液接触的电极片状态也会慢慢恶化[1],所以建议尽量在需要制作扣电的当天再拆解电芯。
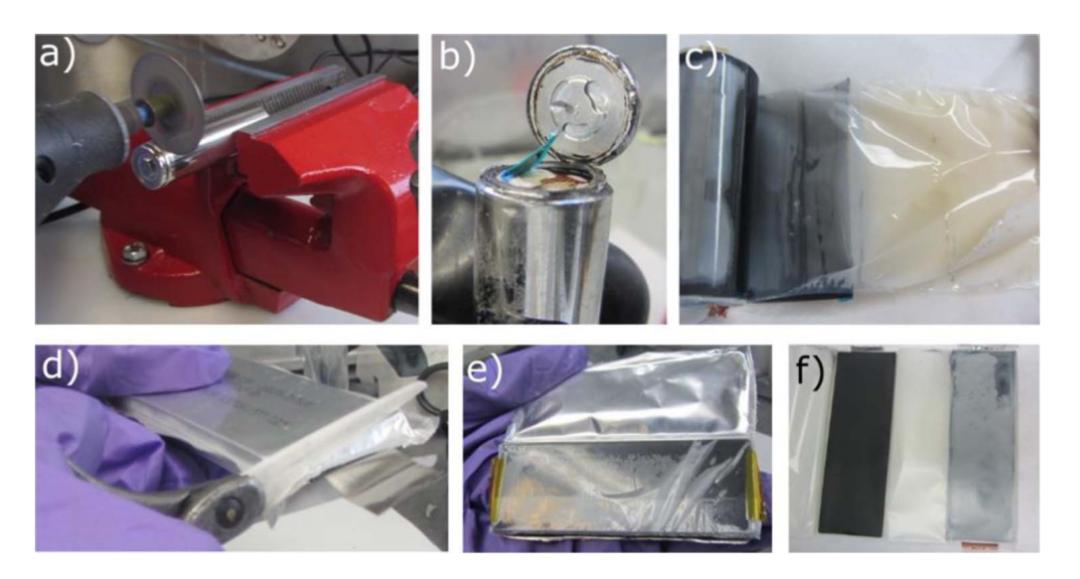
对于扣电制作过程,作者拆解的电芯为94Ah方壳电芯和40Ah的软包电芯,其中隔膜是PP-PE-PP厚度约为25um,电解液成分不相同。扣电制作过程分成2个阶段部分,1)极片清洁和冲片阶段,将双层电极片放在玻璃板上,四周粘贴密封完整,然后使用溶剂浸润电极片表面或者用刀具单纯地刮掉表面,在这里,正负极都是使用NMP作为溶剂的,在清除一面料层之后选择布片擦干表面。在冲片过程中,选择简单的打孔器和EL-CUT两种设备进行裁出直径18mm的正负极片备用。
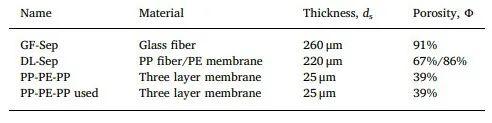
对制作完成之后的扣电进行充电循环测试和EIS电化学阻抗分析测试,通过对比不同样品的测试数据的区别来判断各种因素对扣电制作的影响程度。
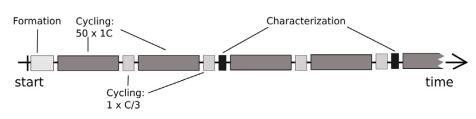
1冲片方式的影响
从下面数据能够看出采用冲子冲出来的1.Gen的容量普遍偏低很多,这说明用冲子冲出来的极片质量较差,边沿不平且受压不均,会导致边沿料层脱落,引起更大电极材料损失。
另外也说明正负极片的对齐度会对扣电的影响非至关重要,因为有扣电的正负极片对齐度是不可能相同的,但是我们得到了非常低的COVc值。
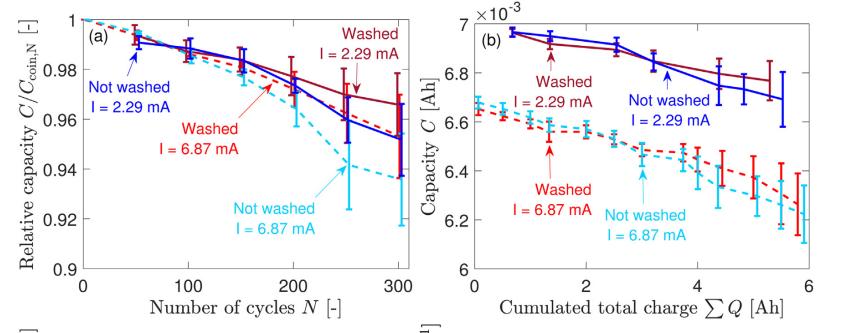

4隔膜的影响通过对比两种类型的隔膜DL-sep和PP-PE-PP的差异,可以发现使用电芯单体里面的自带隔膜的效果会差一些的,更厚的DL-Sep隔膜具有更大的孔隙率,在扣电封口过程中能让扣电的受力更为均匀,提升扣电的电流分布和使用寿命。
通过上述分析,可以对拆解电芯制作扣电过程提供如下的建议
1)拆解电芯后要尽快进行扣电制作
2)冲片时候更可能选择质量好的冲片机器
3)选择合适成分和厚度的隔膜
4)尽可能不用DMC冲洗裁剪后的电极圆片
[1]Journal of The Electrochemical Society, 163 (10) A2149-A2164 (2016)
[2]Journal of Energy Storage 24 (2019) 100732