背景
在数字化的大背景下,电池结构的数字化建模和管控成为研究热点。过去二十年中,层析成像工具的快速发展为研究人员提供了常规表征电池电极微结构的工具。锂离子电池材料的电化学和机械性能很大程度上取决于其三维微观结构特性,了解随机微观结构的定量影响对于预测材料特性和指导合成过程以及结构设计至关重要。
1、电池微结构三维观测
锂离子电池内的三维结构对性能有重要影响。孔相结构会影响液体电解质中锂离子的电导率和扩散率,从而限制电池的充电和放电时间[1]。颗粒大小和形状决定了活性材料的表面积,从而决定了交换电流,这给出了适用的电流倍率上限[2]。活性颗粒的细长形状和宽尺寸分布不仅影响锂离子传输,而且导致颗粒之间和沿厚度方向的电流分布不均匀和锂化不均匀[3]。结构还影响系统的机械响应,并结合材料的弹性特性材料,决定了材料在电荷相关的粒子膨胀和收缩过程中如何变形或断裂[4]。结构特性的异质性导致局部电流负载分布不均,并导致电池退化和老化[5]。因此,结构的准确表示对于确定限制性能的特征和深入了解可能的设计改进至关重要。
捕获电池结构的挑战在于组成材料的异质性,以及它们不同的长度尺度和形态。活性材料颗粒的尺寸通常在数百纳米到数十微米之间,而导电添加剂和聚合物粘合剂的特征尺寸为数十纳米。电池微观结构观测的理想情况是,在一系列时间和空间分辨率以及相关操作环境中以无损方式捕获化学、机械、晶体学和形态学细节。这些跨多个长度尺度的技术使用X射线、电子、中子和离子束,以及光学、红外和其他波长的光来探测电池运行期间的化学异质性和动力学。显微成像技术包括X射线计算机断层扫描(X-ray computed tomography,XCT)、聚焦离子束 (focused ion beam,FIB)-扫描电子显微镜 (scanning electron microscopy,SEM)、TOF-SIMS和基于同步加速器的技术已被用于研究锂离子电池的形态特征,可以通过基于断层扫描重建的材料建模来辅助数据揭示真实的微观结构。微观结构识别后,几何信息可应用于多尺度模型,揭示锂的扩散和降解机制[6]。
2、常用的三维成像方法
目前,最常用的是XCT和FIB-SEM。
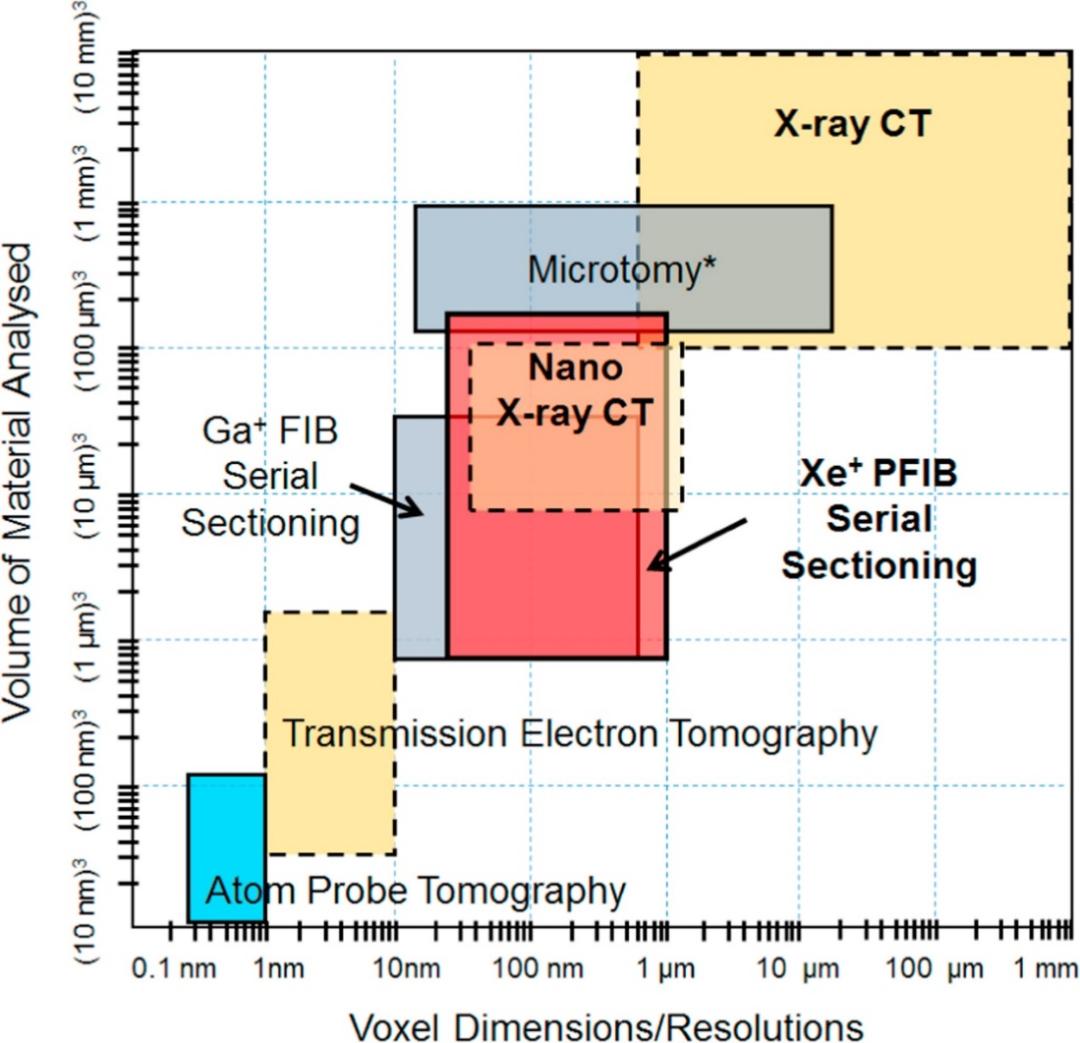
图1 材料科学的3D成像方法
(用虚线表示的非破坏性方法;* - 仅适用于软材料)[7]
(1)X射线计算机断层扫描(X-ray computed tomography,XCT)
近年来,基于X射线的断层扫描分析由于其无损表征电池材料和设备的能力,在锂离子电池研究中受到广泛关注[8,9]。XCT能够提供从毫米到数十纳米的体素大小的一系列分辨率,并且可以进行非破坏性的原位或操作研究,以监测内部电极结构随时间的变化[10]。XCT在单体层面能够研究宏观设计参数和缺陷,在微观结构上可以表征电极微观结构,将电极结构异质性及隔膜孔隙率、迂曲度、平均孔径与性能相关联[11,12]。
尽管 XCT 具有强大的功能,但它通常无法在由具有显着不同X射线衰减特性的材料制成的复合样品中可视化低X射线衰减的材料。由于活性颗粒的X射线衰减相对较高,XCT使CBD与孔隙相难以区分。
X射线微计算机断层扫描 (micro-CT):显示了电池盖中的辅助组件和单体的内部结构,体素尺寸为12.9μm。(图2a)
X射线纳米计算机断层扫描(nano-CT):捕获通过刮刀涂层法分别制备的层状单体的3D微观结构细节,从左到右分别是石墨负极、聚烯烃隔膜和NMC正极的颗粒形状、取向和孔径方面的不同形态。(图2c)
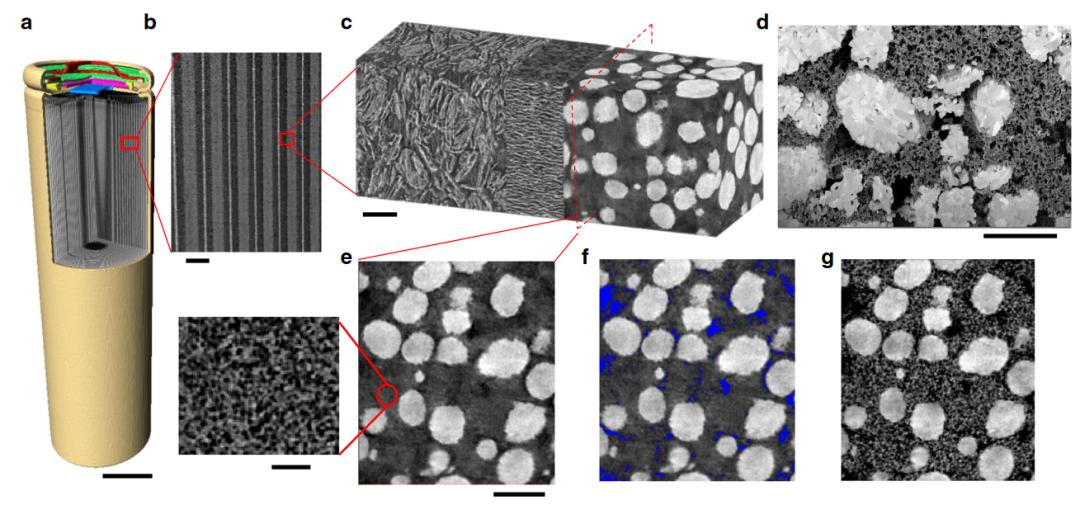
图2:LiB的层次结构[3]
正极:
正极需要分割活性颗粒、CBD和孔隙。
问题:XCT不能区分CBD和孔隙(图2e,体素分辨率126nm),因为两者都具有纳米特征,且碳和孔隙的X射线衰减系数都较低;另外,NMC颗粒高度吸收X射线,进一步降低了CBD对比度水平。
解决方案:二次X射线纳米CT扫描具有更高体素分辨率(63nm)的独立CBD样品(没有NMC颗粒),基于增强的信噪比和更好的空间分辨率和对比度来识别微孔[3,13]。复合得到的图像(图2g)与SEM图像(图2d)的孔隙率和孔径分布对应关系良好。也可以使用机器学习方法进行分割[14]。
应用:原位X射线CT可以研究压延过程中电池电极的微观结构演变,探究颗粒尺寸对电极结构稳定性的影响以及孔隙率和和电极厚度对性能的影响,揭示孔隙率和迂曲度随增量压延步骤的变化[3];研究电池老化,检测正极颗粒开裂和集流体腐蚀[15];建模预测由于循环电压窗口扩大而导致的颗粒开裂增加[16];研究CBD含量和孔隙率对有效传输特性的影响[11]。
负极:
负极需分割石墨颗粒、硅颗粒、CBD和孔隙。
问题:在正极,Li(Ni,Mn,Co)O2等活性材料的颗粒尺寸在1-10μm,并且含有过渡金属元素,在基于吸收的成像过程中提供良好的对比度,因此可以可靠地识别颗粒;而在负极,石墨活性颗粒(商用负极石墨占了很大一部分),没有这种对比度,可能导致分割中的很大误差。
解决方案:多模态成像,高分辨率的ptychographic XCT与分辨率较低但对比度较高的透射XCT显微镜相结合,获得石墨-硅复合负极的3D重建[17]。也可以通过深度学习实现更准确的分割[10]。
应用:对活性颗粒的表面进行定量分析,对分割结构进行电化学模拟,研究颗粒嵌入对局部电荷状态异质性的影响[17];研究电池老化,对导致老化负极孔隙率降低的有机残留物和沉积物进行量化和可视化[15]。

图3 a)用于叠印XCT和透射X射线断层扫描显微镜的激光铣削样品的扫描电子显微镜图像。 b)透射X射线断层显微术和 c)叠层 X 射线计算机断层扫描数据的横截面。 d)两个数据集的叠加,e)多相分割显示灰色的石墨颗粒、蓝色的硅颗粒和橙色的CBD。 f)相同的颜色代码用于电极的3D表示。
隔膜:
孔隙率和迂曲度是表征与锂离子通过隔膜传输相关的隔膜性能的重要参数,分割隔膜微结构能够用于表征锂离子电池隔膜的几何特性。
问题:纳米级XCT(~100 nm)分辨率相对较低的限制,聚合物隔膜的原纤维 (< 100 nm) 无法在基于图像的模型中捕获。
解决方案:将原纤维添加到基于图像的模型中,使用实验应力-应变曲线和从SEM获得的图像进行验证[19]。也可以将FIB-SEM 信息与XCT数据相结合[18]。
应用:分析确定锂离子电池隔膜在压缩状态下的孔隙率和曲折度之间的关系,用于分析变形隔膜的锂离子电池的性能[19];分析隔膜的传输特性[18]。
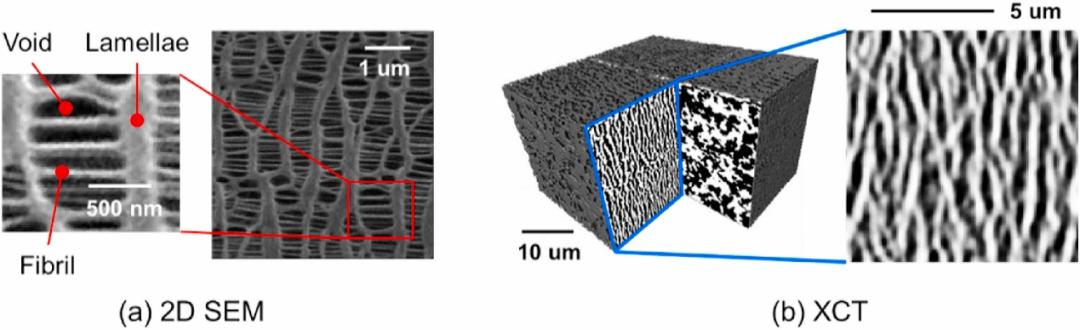
图4:隔膜SEM与XCT[18]
(2)FIB-SEM与PFIB-SEM
XCT在空间分辨率和成像对比度方面受到限制,无法区分碳粘合剂结构域(CBD)和孔隙。聚焦离子束扫描电子显微镜(FIB-SEM)是一种将用于材料加工的离子束和用于成像的电子柱相结合的分析方法,支持具有纳米空间分辨率的2D和3D成像[7],具有分辨所有三相(活性颗粒、CBD 和孔隙)的能力。传统的Ga+ FIB-SEM已广泛用于电池材料,包括界面/相间表征、3D量化和基于计算模拟的分析。
但是FIB-SEM的采集时间很长,需要在有限视野和高分辨率之间权衡,并且具有破坏性,因此,在微观结构3D重构方面不像XCT那样常用。尽管如此,FIB-SEM提供了一种替代探针,通常具有不同的对比度生成机制和更高的空间分辨率,能够对非破坏性3D成像技术识别的体积进行特定位置的提取,以进行后续更高分辨率的检查。目前FIB-SEM通常用于正极的三维表征,指导电极设计。
因为厚电极的降解过程与不同长度尺度下的结构和化学复杂性密切相关。在评估厚电极中不同成分(包括孔隙、活性材料、碳添加剂和粘合剂)的复杂形态和互连性质时,需要进行完整的3D表征。有关厚电极的详细3D结构和化学信息对于量化和模拟不均匀性也至关重要[20]。FIB只能探测数十微米的深度和体积,研究厚电极需要一种具有FIB特定位置精度但能够连续切片更大的体积的工具。等离子Xe+ FIB能够铣削数百微米长度的材料。
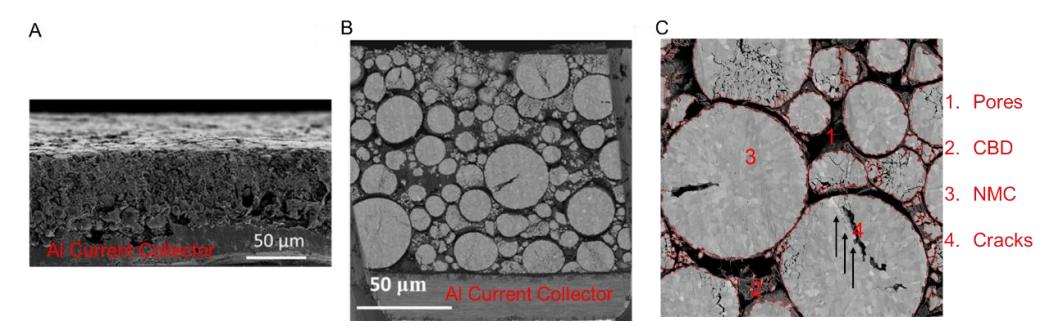
图5 (A) NMC811厚电极的SEM横截面图像。(B) PFIB大体积连续段的厚电极。(C) 用PFIB-SEM数据计算的组件分割。
新兴的等离子体FIB-SEM(PFIB-SEM)技术最近被开发出来。与Ga+相比,等离子的离子源更宽但准直,使得在μA范围内实现电流成为可能[21]。由于通过比Ga+系统快40倍的研磨速率访问具有代表性的2D区域和3D体积[20],PFIB-SEM技术有望在电池材料表征方面发挥巨大潜力。此外,PFIB-SEM可通过非反应离子源(Xe+和Ar+)在先进电池系统上进行无Ga+样品制备。
应用:用于研究NMC811衰减机制,观察颗粒开裂,评估活性颗粒中裂纹的影响[22];研究颗粒和CBD之间的接触损失与电池单体衰减的相关性,量化循环引起的CBD脱离[23],电子和离子传输网络在厚正极性能劣化中的作用[20];研究CBD体积分数及其形态对电极传输特性的影响[11]。
参考文献
1. Delattre, B. et al. Impact of Pore Tortuosity on Electrode Kinetics in Lithium Battery Electrodes: Study in Directionally Freeze-Cast LiNi0.8Co0.15Al0.05O2 (NCA). J. Electrochem. Soc. 165, A388 (2018).
2. Kayyar, A., Qian, H. & Luo, J. Surface adsorption and disordering in LiFePO4 based battery cathodes. Appl Phys Lett 95, 221905 (2009).
3. Lu, X. et al. 3D microstructure design of lithium-ion battery electrodes assisted by X-ray nano-computed tomography and modelling. Nat Commun 11, 2079 (2020).
4. Li, A., Hempel, J., Cheng, Y.-T. & Taub, A. Effect of Binder Content on Silicon Microparticle Anodes for Lithium-Ion Batteries. Meet. Abstr. MA2022-01, 423–423 (2022).
5. Xu, R. et al. Heterogeneous damage in Li-ion batteries: Experimental analysis and theoretical modeling. J Mech Phys Solids 129, 160–183 (2019).
6. Liu, X. et al. Bridging Multiscale Characterization Technologies and Digital Modeling to Evaluate Lithium Battery Full Lifecycle. Adv Energy Mater 12, 2200889 (2022).
7. Burnett, T. L. et al. Large volume serial section tomography by Xe Plasma FIB dual beam microscopy. Ultramicroscopy 161, 119–129 (2016).
8. Pietsch, P. & Wood, V. X-Ray Tomography for Lithium Ion Battery Research: A Practical Guide. Annu Rev Mater Res 47, 451–479 (2017).
9. Ebner, M., Geldmacher, F., Marone, F., Stampanoni, M. & Wood, V. X-Ray Tomography of Porous, Transition Metal Oxide Based Lithium Ion Battery Electrodes. Adv Energy Mater 3, 845–850 (2013).
10. Müller, S. et al. Deep learning-based segmentation of lithium-ion battery microstructures enhanced by artificially generated electrodes. Nat Commun 12, 6205 (2021).
11. Ghadban, M. et al. 3D microscale modeling of NMC cathodes using multi-resolution FIB-SEM tomography. J Power Sources 562, 232745 (2023).
12. Finegan, D. P. et al. Characterising the structural properties of polymer separators for lithium-ion batteries in 3D using phase contrast X-ray microscopy. J Power Sources 333, 184–192 (2016).
13. Lu, X. et al. Microstructural Evolution of Battery Electrodes During Calendering. Joule 4, 2746–2768 (2020).
14. Jiang, Z. et al. Machine-learning-revealed statistics of the particle-carbon/binder detachment in lithium-ion battery cathodes. Nat Commun 11, 2310 (2020).
15. Rahe, C. et al. Nanoscale X-ray imaging of ageing in automotive lithium ion battery cells. J Power Sources 433, 126631 (2019).
16. Boyce, A. M. et al. Cracking predictions of lithium-ion battery electrodes by X-ray computed tomography and modelling. J Power Sources 526, 231119 (2022).
17. Müller, S. et al. Multimodal Nanoscale Tomographic Imaging for Battery Electrodes. Adv Energy Mater 10, 1904119 (2020).
18. Xu, H., Usseglio-Viretta, F., Kench, S., Cooper, S. J. & Finegan, D. P. Microstructure reconstruction of battery polymer separators by fusing 2D and 3D image data for transport property analysis. J Power Sources 480, 229101 (2020).
19. Sun, W. & Li, Q. M. Understanding the microstructure behaviour of the Li-ion battery separator under compression using 3D image-based modelling. International Journal of Mechanical Sciences 216, 106976 (2022).
20. Zhang, M. et al. Coupling of multiscale imaging analysis and computational modeling for understanding thick cathode degradation mechanisms. Joule 7, 201–220 (2023).
21. Smith, N. S. et al. High brightness inductively coupled plasma source for high current focused ion beam applications. J. Vac. Sci. Technol. B 24, 2902 (2006).
22. Wilson, J. R., Cronin, J. S., Barnett, S. A. & Harris, S. J. Measurement of three-dimensional microstructure in a LiCoO2 positive electrode. Journal of Power Sources 196, 3443–3447 (2011).
23. Liu, H. et al. Three-dimensional investigation of cycling-induced microstructural changes in lithium-ion battery cathodes using focused ion beam/scanning electron microscopy. J Power Sources 306, 300–308 (2016).
文案:陶思怡
排版:张浩宇